When Tsah Yahav and his team began to deconstruct a former military hospital on a three-hectare site near Grenoble, a city in the south east of France, it was far from a classic image of demolition.
They didn’t deploy bulldozers or excavators. There weren’t any wrecking balls or controlled explosions.
Instead, the team of a dozen workers went about their labor using handheld tools.
“It was very manual work,” says Yahav, who led the eight-month project that began in February 2021. “It took a bit more time to deconstruct things carefully.”
The site, known as Le Cadran Solaire (The Sundial), had been earmarked by regional authorities for a unique experiment to pilot a new way of reusing buildings and the valuable physical resources within them after their initial intended use.
Their goal was to salvage as much material as possible from the site — including radiators, stones, bricks, tiles, door frames and handles — that would otherwise have been thrown away, usually buried or incinerated, and to give it a second life.
“We shouldn’t see these things as waste, but as resources,” explains Yahav.
For some years, Grenoble had been considering different ways in which to make its local construction industry more sustainable.
For one, there is a pressing need to find a better model: Raw material extraction, manufacturing and construction account for up to 12 percent of greenhouse gas emissions and over 35 percent of the total waste generated in Europe. (The European Commission estimates that more efficient use of materials could cut 80 percent of those emissions.)
Weighed down by negative news?
Our smart, bright, weekly newsletter is the uplift you’ve been looking for.
But they were also legally obliged to: Under the French anti-waste law for a circular economy (AGEC), which came into force in 2020 after years of development, some 70 percent of most non-hazardous building waste had to be collected for processing in France. The objective is gradually rising, too: In 2024, the target was 82 percent, and it will increase to 93 percent by 2027.
So Le Cadran Solaire, which is being transformed into a mixed-use site for university premises, housing and more, was chosen by Grenoble authorities as an opportunity to measure and compare the financial, temporal, environmental and social impacts of “classic demolition” versus so-called “selective deconstruction” with a view to reuse.
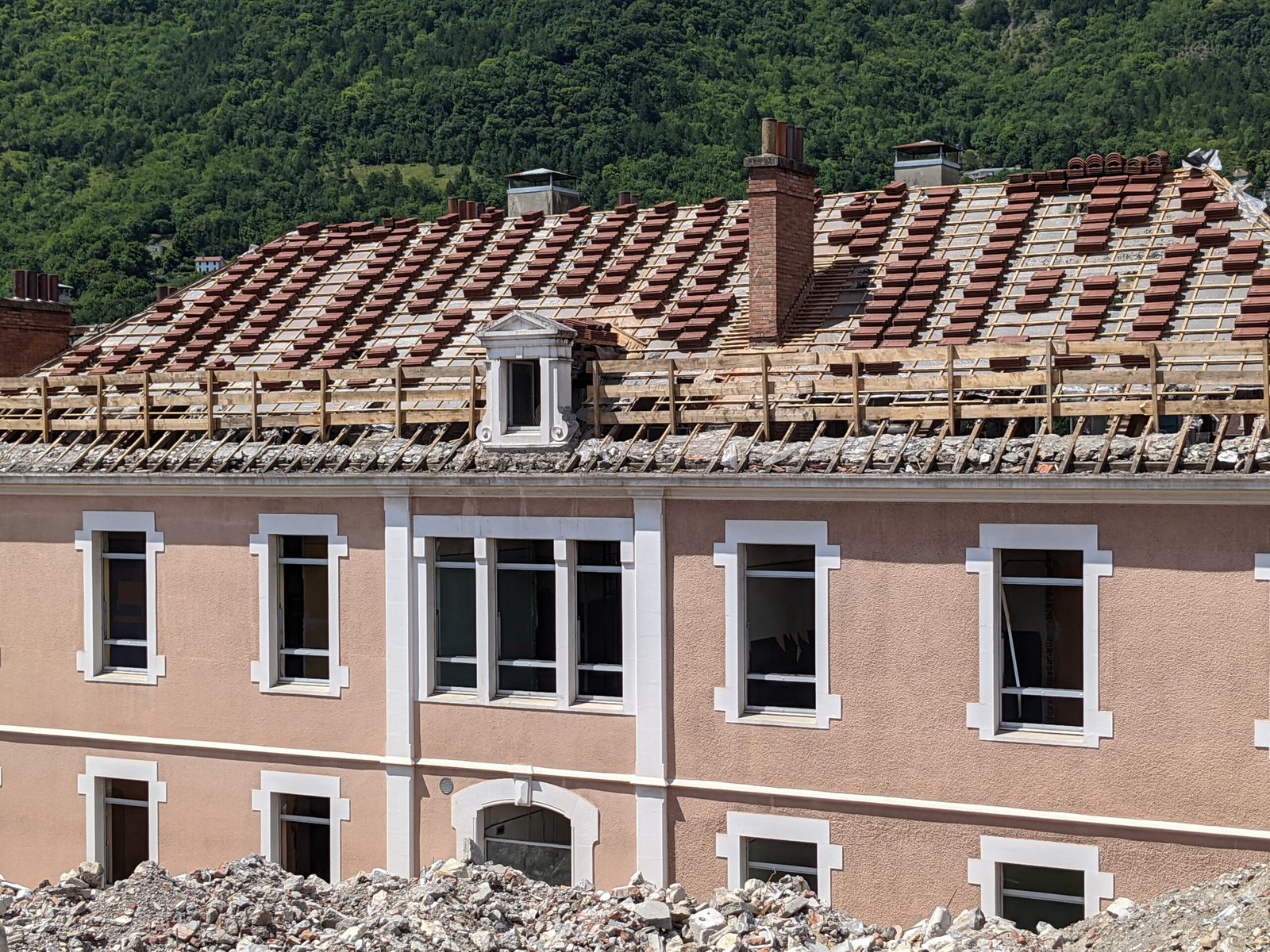
The buildings on the 100-year-old site were almost identical in terms of furniture, interior finishes, plumbing, electricity and structure. So four of them were chosen for selective deconstruction and two for classic demolition as a baseline comparison.
The project was entrusted to Ecomat 38, a nonprofit and specialist in this selective removal and reuse of materials.
Crucially, their efforts focus on direct reuse of objects rather than recycling.
“We aren’t speaking about taking a window, smashing it and creating another window out of it,” says Didier Grand, a longtime employee and head of communications. “We keep the panes intact. We want things to be reused immediately, which reduces waste.”
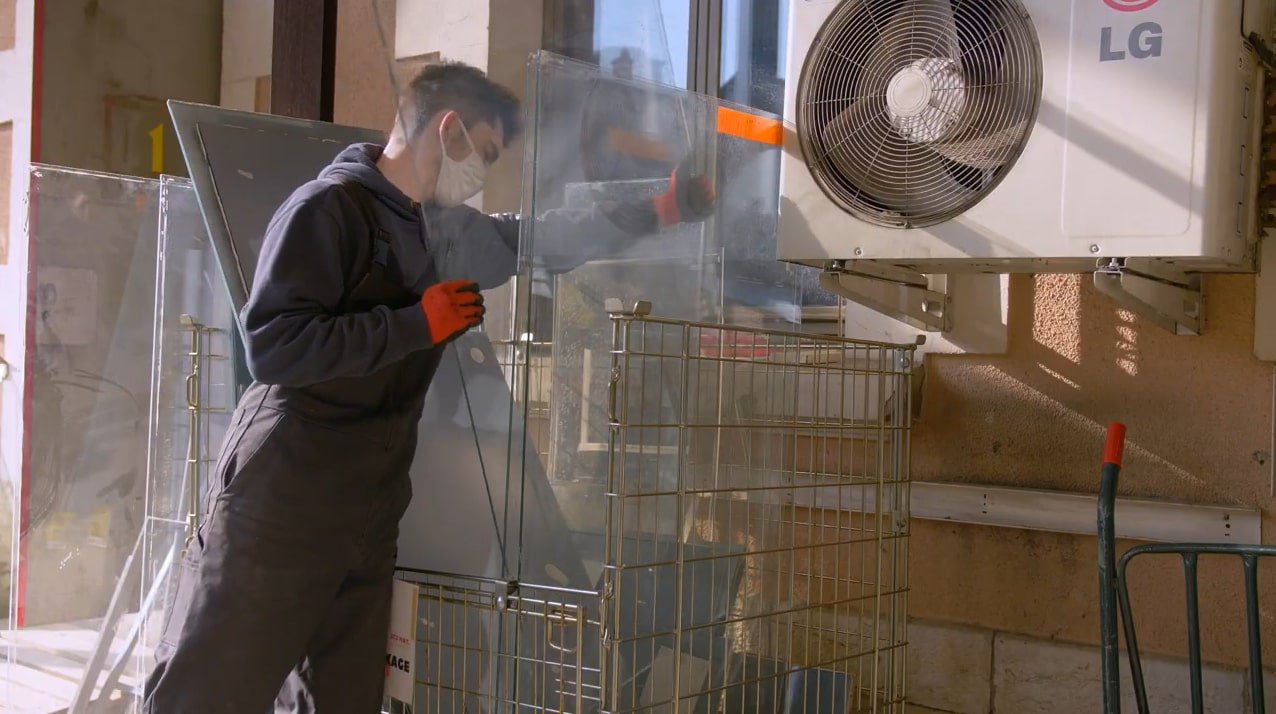
Before deconstruction began, Ecomat 38’s team, working with architecture company NA ! and a number of other organizations, carried out three “resource diagnostics” on the site, a key part of the process to identify what could likely be reused.
Then came the deconstruction, which had to be carefully done to minimize damage. Each building took a couple of weeks. In the end 320 metric tons of material were collected, including 50 metric tons of tiles and 70 metric tons of wood. The resources were either stored to be reused in the upcoming construction or sold in an on-site pop-up store, the Batitec, which was open to the public on weekends for five months.
“Some customers came for the cheap prices, others because of the ecological philosophy,” says Yahav.
Either way, the deconstruction of Le Cadran Solaire was a resounding success. The project, having set a target of recovering 85 percent of materials — 15 percent more than is currently required by France’s AGEC law — actually achieved 98 percent.
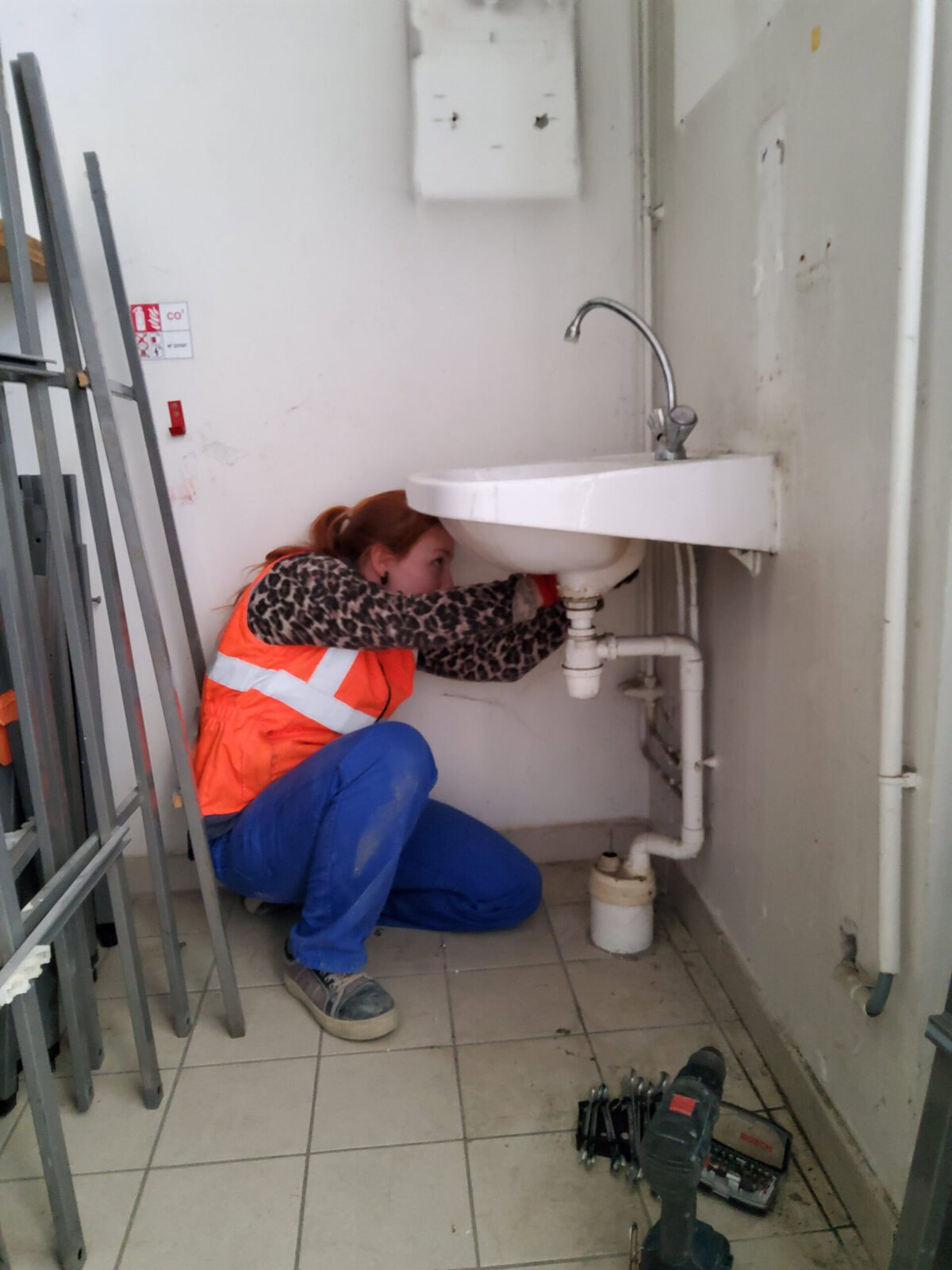
The project also led to the hiring of 12 full-time employees — and by the end six of them were given a permanent contract with Ecomat 38, underlining the job creation potential of this emerging green economy.
The overall cost was even 40 percent cheaper, linked to the cost of waste avoided by reuse in situ, compared to conventional demolition.
And according to Ecomat 38’s calculations, the selective deconstruction reduced the CO2 emissions by 373 metric tons of carbon, the equivalent of producing 16,000 pairs of jeans or flying around the world 39 times in an airplane.
Nonetheless, selective deconstruction, as expected, required more time. Ecomat 38 says 70 percent more. However, this difference did not have an impact on the overall timeline since the companies planned and coordinated for this: They staggered the asbestos removal, selective cleaning and demolition work on the different buildings.
“We learned a lot,” says Yahav. “It was the first big deconstruction in the public market in France.”
Since then, Ecomat 38 has been involved in dozens of other selective deconstruction projects in the Auvergne-Rhône-Alpes region, including a post office, a train station, a tourist office, restaurants, offices and more. In the meantime, it has also opened a permanent store for sales of reclaimed materials from all kinds of building sites.
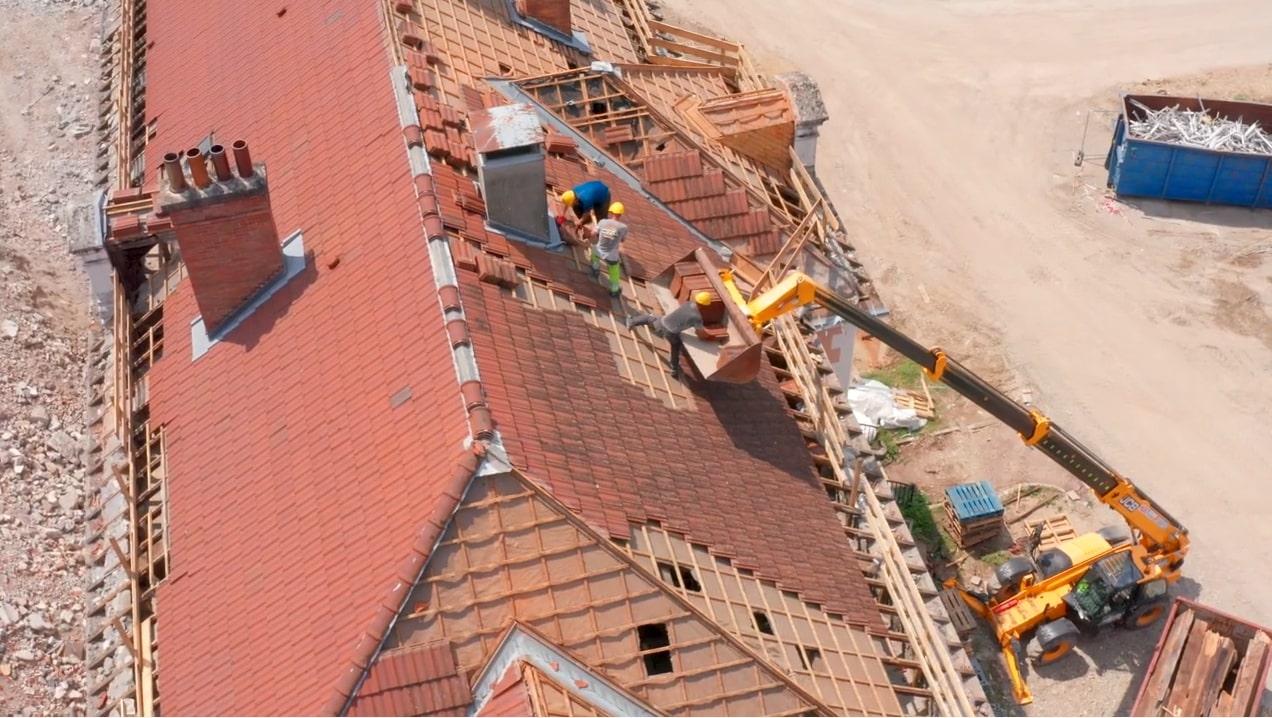
Yet there is still a massive way to go. France produces 42 million metric tons of waste from building construction each year. Meanwhile, the US Environmental Protection Agency estimated that 600 million tons of construction and demolition debris were generated in the United States in 2018 — with 90 percent of that due to demolition.
“The reality is that right now we don’t deconstruct buildings, we demolish them,” says Felix Heisel, an assistant professor of architecture and director of the Circular Construction Lab at Cornell University.
For Heisel, there is a significant difference between demolition and deconstruction — the latter he calls “a systematic dismantling of a building … to recover material at its highest utility and value.”
“By retaining these building materials and allowing them to be reused, we don’t need to produce new materials,” he adds. “Reuse is a very local approach, it puts value in local labor and local economies.”
In fact, Heisel believes selective deconstruction is something of a return to the past.
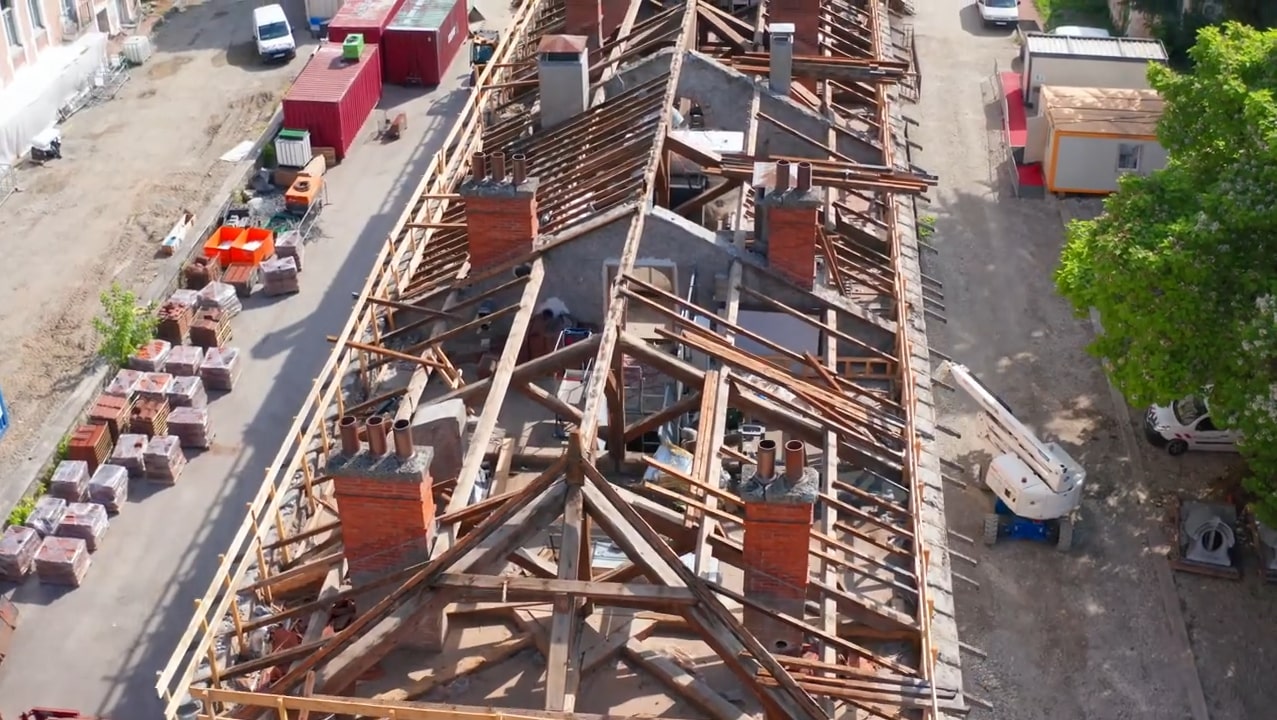
Before industrialization, it was the norm to re-employ materials locally as much as possible. “But World War II brought the bulldozer, which was used as a means of clearing,” he explains. “Now we’re reinventing deconstruction, trying to implement it in an industrialized world. It’s an interesting possible new green workforce.”
Heisel’s own research found that deconstruction can be economically viable and time competitive. In 2022, as part of the Catherine Commons Deconstruction Project, a crew of eight workers methodically deconstructed a 420-square-meter building, one of 11 residential structures set to be demolished in Ithaca, New York, in five days.
According to a 2024 report by the Circular Construction Lab, converting half to three-quarters of residential building demolitions to deconstructions in New York State could create 8,130 to 12,630 jobs, reclaiming 270,000 to 420,000 tons of materials and producing a direct economic impact of $872 million to $1.4 billion.
Yet to scale up, there’s a lot of hard graft ahead.
While the European Union has pushed ahead with policy, introducing its first Circular Economy Action Plan in 2015 and requiring higher rates of waste separation from construction companies, Grand believes that the market and wider economic model don’t yet properly exist for reuse or re-employment on a national level.
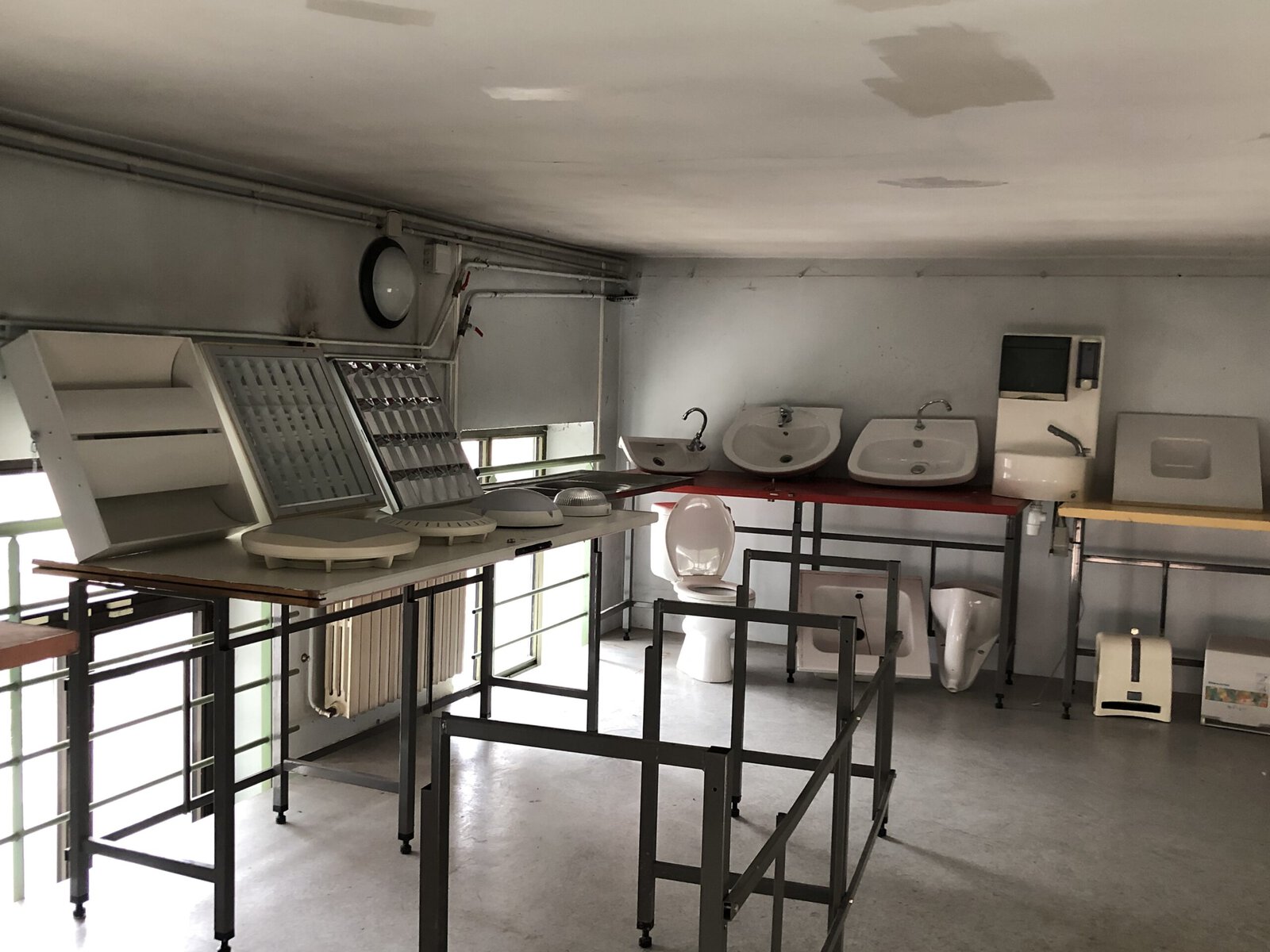
“We still need to have access to more worksites, places to sell what we recover and to find an economic model that works,” he says. “The reality is that it’s cheaper to buy new things than reuse old ones.”
Professor Heiseil agrees. “To really scale this, to make it economically competitive, we have to build the market infrastructure for it, the demand to do it, and to build the capacity for a workforce that can actually do the deconstruction,” he says.
Other factors include that U.S. residential building stock largely is made of timber, which means deconstruction could be different (and potentially easier), when compared to the largely concrete homes in Europe. The development of insurance and material passports for reclaimed materials, as well as points of sale, are key.
But that ecosystem is already beginning to be built.
In 2022, San Antonio, Texas, the seventh-largest city in the U.S., introduced its own deconstruction ordinance, requiring certain projects to be “fully deconstructed” as opposed to mechanically demolished. In 2023, the city of Boulder, Colorado, used the steel from a 250,000-square-foot hospital to build a new fire station. And back in Grenoble, working groups have been set up for public building owners interested in implementing the new practices across the Auvergne-Rhône-Alpes region.
“This work changed my life,” says Yahav, of Ecomat 38. “I buy as few new things as possible, even clothes. It’s changed the way I see the world.”
The post By Deconstructing Buildings With Care, Materials Get a Second Life appeared first on Reasons to be Cheerful.